

Artificial intelligence (AI) and machine learning (ML) will deliver greater automation and improved data flow between software systems and manufacturing equipment, making it possible for those with even minimal expertise to successfully program and operate machine tools.
#Cad cam works manual
PMI will be especially important as the current generation of workers retire, he added, suggesting that the next generation will be unwilling to work with the lower level of detail and manual data input common in today’s classic CAM products. “If you want to eliminate paper on the shop floor and really streamline the manufacturing process, it starts there, with PMI data,” said Mathews. There’s one big hurdle to its widespread adoption, though: educating design engineering teams to properly and fully document the geometry of the workpiece. PMI is described in ASME Y14.41-2019, Digital Product Definition Data Practices. A CAM system can harvest the data within to generate smarter toolpaths, for example, just as CAI (computer-aided inspection) might use it to generate a first-article inspection plan. Because the information conveyed through MBD and its subset PMI are machine-readable, interoperability becomes much easier. This concept is known as a model-based definition (MBD), an important piece of the Industry 4.0 puzzle. When married to a 3D CAD model, PMI eliminates the need for a 2D part drawing. It includes geometric dimensioning and tolerancing (GD&T) information, material specifications, design annotations, surface finish requirements, engineering change orders, and any other digital data associated with the part or assembly. As he and others explained for this article, PMI refers to all of the design, quality, and manufacturing-related data-or metadata-that can and should accompany a 3D CAD model.
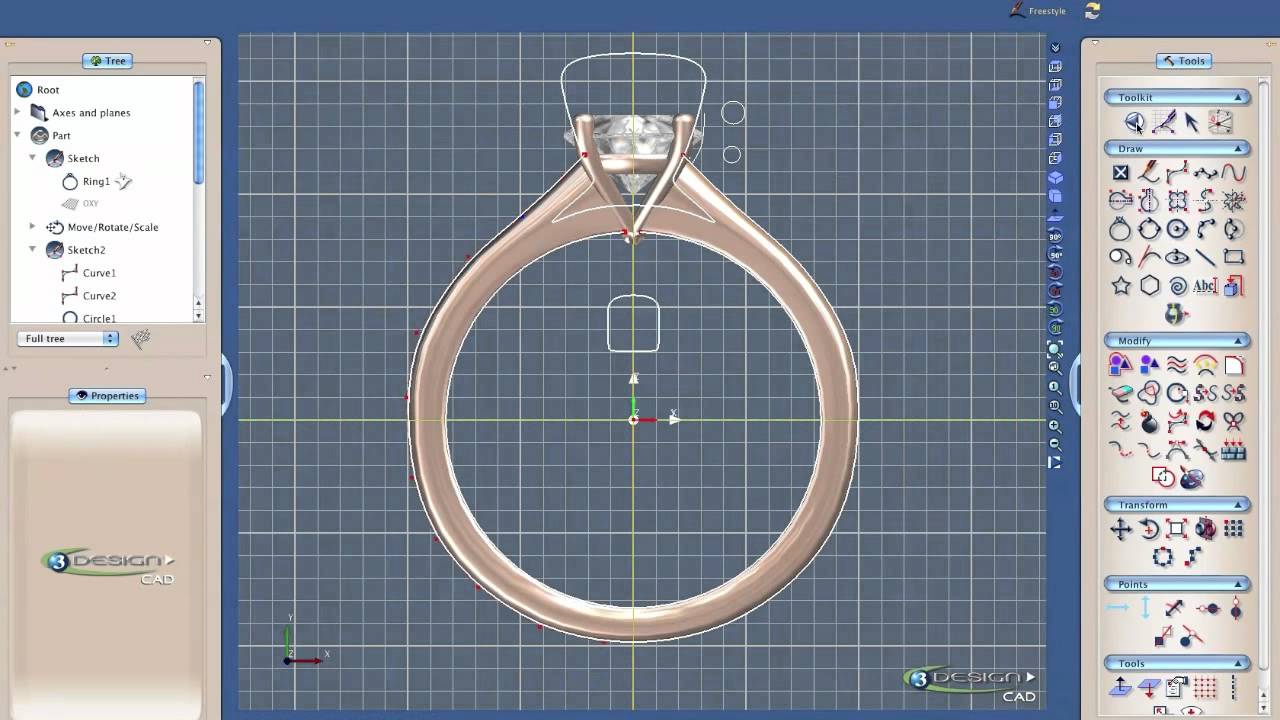
Mathews noted that one key element of this data is product manufacturing information (PMI). Now, we’re able to leverage it much earlier in the process, using digital twin data to generate part programs that provide shorter cycle times and longer tool life.” “In the past, application of the digital twin within a machining environment was primarily limited to post-processed G-code simulation. He started by saying that manufacturers are most likely to succeed on their interoperability journey by first adopting a CAM-centered workflow, one with the digital twin as its foundation. Chuck Mathews, executive vice president of ESPRIT CAM, Camarillo, Calif., part of Hexagon’s Manufacturing Intelligence Division, has thoughts on all of them. Must shops now hire a software developer or two to augment their team of CAD/CAM programmers? Once these systems are talking, what information should they be made to share? Which will serve as the master, or system of record? And what happens when one or more of them requires a routine update? Goodbye, Paper
#Cad cam works how to
The challenge, then, is how to get these disparate software systems to speak to one another.
#Cad cam works Offline
Toolpath simulation and optimization, machine tool monitoring, electronic work instructions, offline presetting and tool management systems (TMS), cloud-based tooling libraries, inline probing and metrology, manufacturing execution systems (MES)-companies everywhere have either implemented or are in the process of implementing these and other manufacturing systems, raising countless improvement opportunities for those willing to tackle such transformative projects. In this age of interoperability, however, effective toolpaths are only part of the machine shop best practices story. Perhaps most importantly, a well-oiled CAD/CAM system significantly increases shop floor efficiency, providing shorter cycle times and fewer chances of a costly mistake during machine setup. Chief among these are accurate, productive toolpaths, resulting in improved tool life, greater equipment uptime, and reduced wear and tear on humans and machinery alike. Yet most manufacturers today would agree that investment in a modern CAD/CAM system-one driven by knowledgeable, well-trained programmers-brings numerous benefits to the shop floor, manual programming abilities notwithstanding. It wasn’t so long ago that machinists programmed CNC lathes and mills by hand. (Provided by DP Technology/Hexagon Manufacturing Intelligence) Designer CAD for CAM software, by Hexagon’s Manufacturing Intelligence Division, simplifies the transition from design to manufacturing by ensuring that manufacturability is central to workflow.

Today’s CAD/CAM software is not only expected to construct the very best toolpaths and machining plans, but must also be interoperable with software from partner companies and other third-party vendors.
